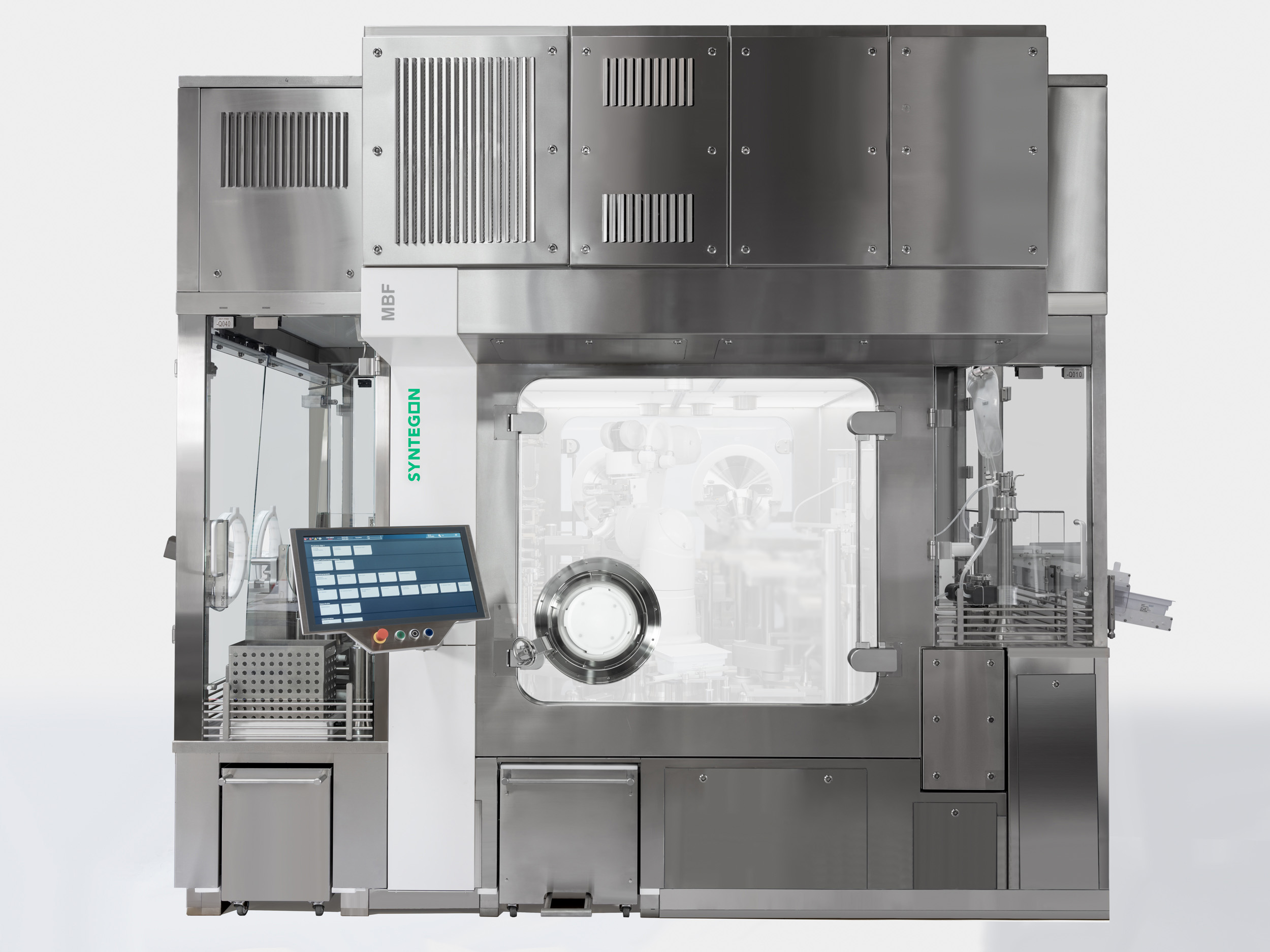
Der Vortrag beschäftigt sich mit der Evolution von Isolatoren in der Pharmaproduktion, wie diese charakterisiert sind, also aus welchen Bestandteilen ein Isolator zusammengesetzt ist und welche Aufgaben ein Isolator in seiner Anwendung erfüllt. Beim Einsatz von Isolatoren im Bereich der pharmazeutischen Abfüllung von aseptischen oder hochwirksamen Produkten sind Isolatoren mit den jeweiligen Füllmaschinen verbunden und folglich ist es wichtig, dass die Schnittstellen zwischen Füllmaschine und Isolator optimal aufeinander abgestimmt sind. Dies gelingt am besten mit integrierten Systemen von einem Hersteller, bei denen bereits in der Entwicklung die Füllmaschinen mit dem Prozess des Isolators abgestimmt werden. Um den Anforderungen der Anwender gerecht zu werden haben sich Isolatoren in den letzten Jahren stark weiter entwickelt – sowohl im Bereich der Zykluszeiten, als auch in der Bauweise. Durch den Einsatz von integrierter Lüftungstechnik können die Isolator Anlagen wesentlich kompakter gebaut werden und somit ergeben sich viele Vorteile für den Nutzer, da es keiner zusätzlichen „air handling units“ in den gesonderten Technikbereichen bedarf. Die bisher höchste Evolutionsstufe ist das Erreichen des Meilensteins einer handschuhlosen Produktion ohne jegliche Bedienereingriffe am Isolator. Für Kleinchargenproduktion kann der Produktionsprozess inkl. dem aseptischen Rüsten und auch dem Umgebungsmonitoring vollautomatisiert erfolgen, ohne dass ein Bediener über Handschuhe in den Produktionsprozess eingreifen muss. Wissend, dass der Mensch die kritischste Quelle einer möglichen Kontamination ist, ist es ein erheblicher Qualitätszugewinn und eine merkliche Reduzierung von Risiken, wenn „gloveless isolators“ zum Einsatz kommen.
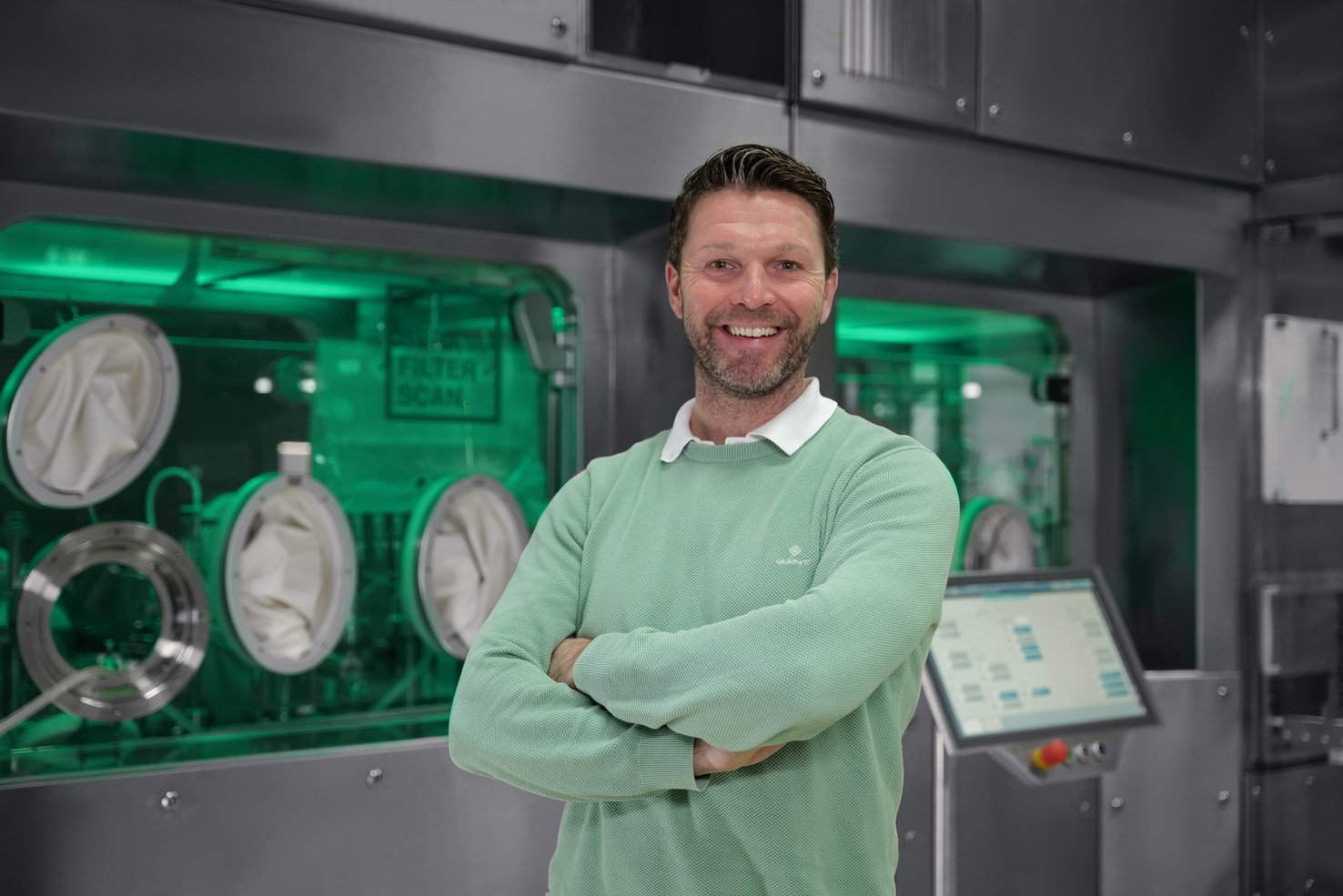