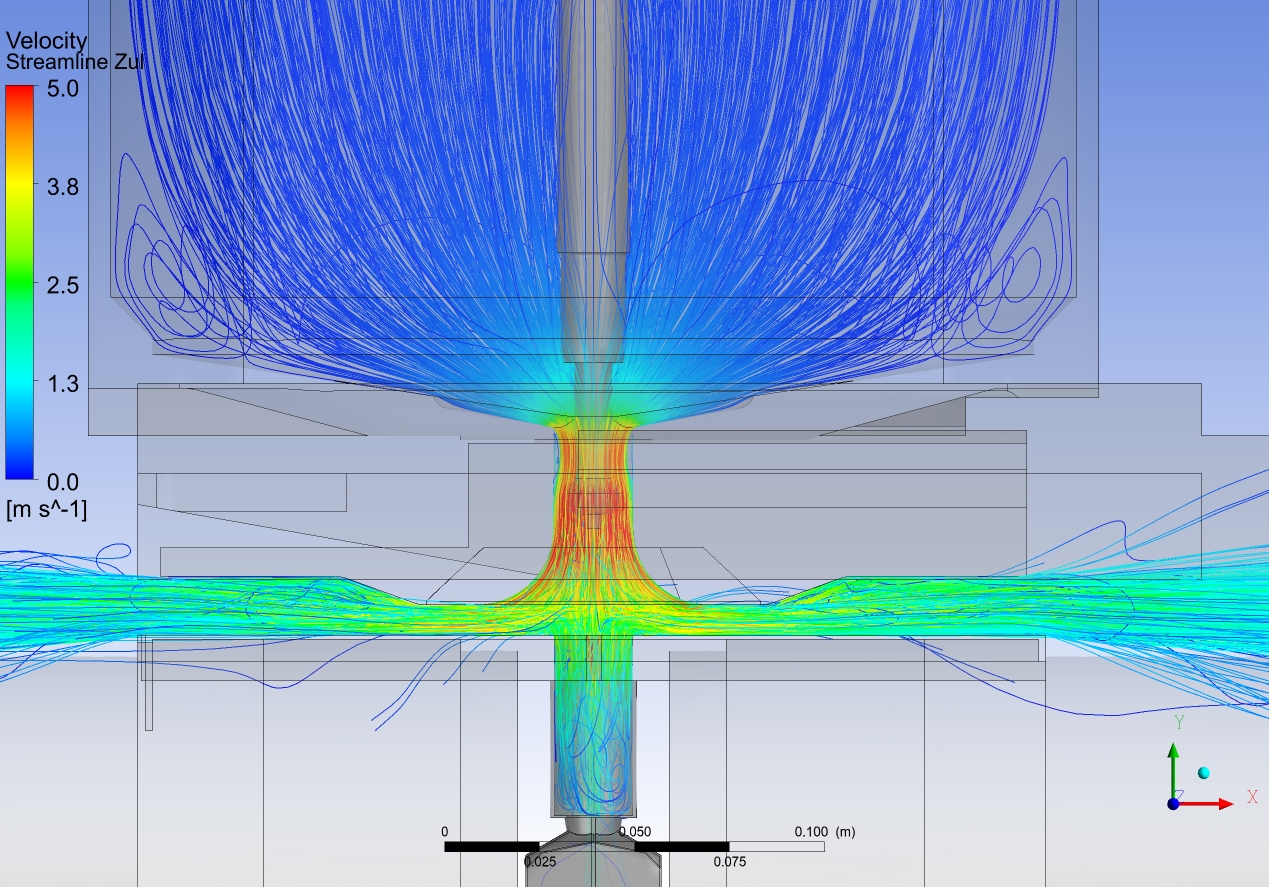
Häufig werden erst bei der Strömungsvisualisierung am fertigen Reinluftsystem unerwünschte Strömungsverläufe erkannt.
Dabei kann es sich um Verwirbelungen, Richtungsumkehr, stehende Luft und ähnliche unerwünschte Effekte handeln, die zu einer Kontamination des Produkts führen können.
Ein bereits installiertes Reinluftsystem nachträglich zu optimieren, ist oft mit viel Zeit- und Kostenaufwand und im schlimmsten Fall mit Produktionsstillstand verbunden.
In manchen Fällen ist eine nachträgliche Optimierung nicht mehr realisierbar. Daher empfiehlt es sich, für komplexe Reinluftsysteme, bei denen die Strömungsverläufe nicht einfach vorhersehbar sind, bereits in der Designphase eine Strömungssimulation am Rechner durchführen zu lassen. Dadurch ist es möglich, vor dem Bau der Anlage, schwerwiegende Fehler zu vermeiden und damit dem Kunden eine Menge Kosten und Ärger zu sparen.
Auch für Bestandsanlagen kann vorab eine Optimierung per CFD erfolgen und überprüft werden, ob die Optimierungsmaßnahme zum gewünschten Ergebnis führt, bevor der Umbau erfolgt.
Herr Kuhn zeigt verschiedene Praxisbeispiele zur CFD-Simulation und deren Mehrwert in der Reinraumtechnik. Unter anderem kann die Energieeffizienz durch eine qualitativ hochwertige Simulation positiv beeinflusst werden.
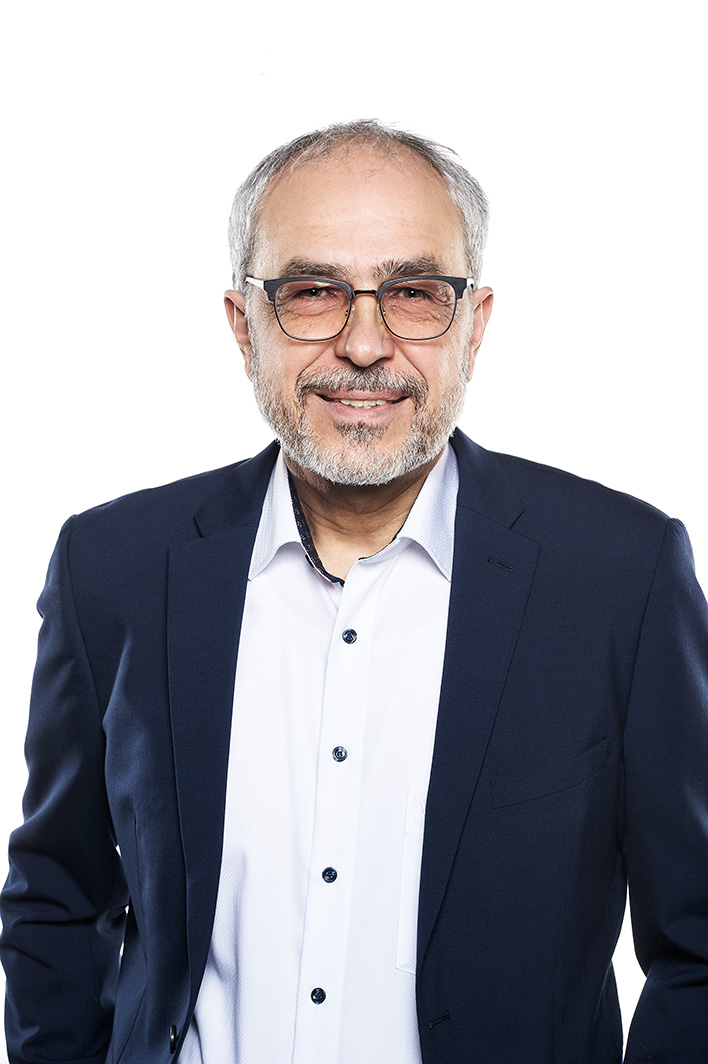