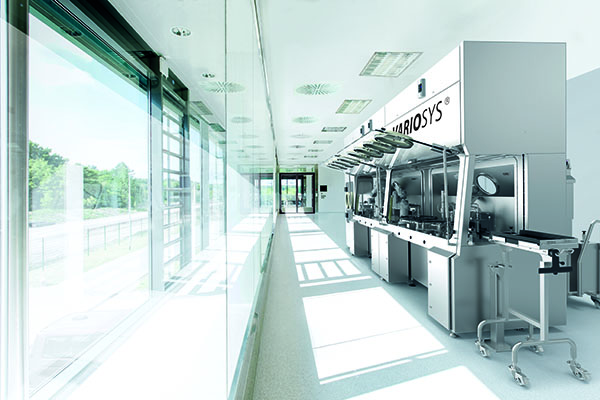
Die Pharmaindustrie steht vor der Herausforderung, den steigenden Bedarf an flexiblen und vielseitigen Fertigungsprozessen zu decken, um eine breite Palette von Pharma-Produkten effizient herzustellen.
In diesem dynamischen Umfeld gewinnen flexible Abfüll- und Verpackungsanlagen zunehmend an Bedeutung.
Vorsterilisierte Verpackungen sind seit langem ein wesentlicher Bestandteil der pharmazeutischen Produktion. Insbesondere RTU-Spritzen (Ready-to-Use) haben sich aufgrund ihrer zahlreichen Vorteile etabliert. Der Fokus auf den Kernprozess des Abfüllens pharmazeutischer Produkte hat dazu geführt, dass vorgelagerte Prozessschritte wie Reinigung und Sterilisation immer mehr ausgelagert werden. In den letzten Jahren haben auch RTU-Vials und Karpulen diesen Trend übernommen. Die Vermeidung von Glas-zu-Glas-Kontakt und die Flexibilität bei der Verarbeitung verschiedener Verpackungsmaterialien auf einer Maschine sind hierbei von zentraler Bedeutung.
Diese Trend wird durch die zahlreichen Vorteile von RTU-Objekten, wie geringere betriebliche Risiken, höhere Flexibilität und Effizienz sowie reduzierte Gesamtbetriebskosten, vorangetrieben. Aktuelle Studien deuten darauf hin, dass die Verwendung von RTU-Objekten in der Pharmaindustrie in den kommenden Jahren weiter zunehmen wird.
RTU-Objekte bringen jedoch auch Herausforderungen mit sich, wie den sterilen Transfer in den Reinraum und Inspektionsprozesse wie 100% IPC (In-Process Control) oder Bördeln. Ein neuer Ansatz im Bereich der Kleinchargenabfüllung bietet innovative und zukunftsweisende Lösungen, die diesen Herausforderungen begegnen. Die sich ständig wandelnde Pharmabranche erfordert kontinuierliche Anpassungen und Entwicklungen, um neuen Prozessen und Anforderungen gerecht zu werden. Flexibilität ist hierbei der Schlüssel zum Erfolg.
Flexible Mehrprodukt-Abfüll- und Verpackungsanlagen bieten zahlreiche Vorteile, die es pharmazeutischen Unternehmen ermöglichen, ihre Effizienz, Flexibilität und Gesamtproduktivität zu steigern. Zu den wichtigsten Vorteilen gehören:
1. Breites Produktspektrum: Diese Anlagen können eine Vielzahl von pharmazeutischen Produkten verarbeiten, einschließlich Flüssigkeiten und lyophilisierten Produkten. Diese Vielseitigkeit ermöglicht es Herstellern, verschiedene Präparate ohne umfangreiche Umrüstung oder Neukonfigurierung der Anlage herzustellen.
2. Reduzierte Umrüstzeiten: Der modulare Aufbau und die Anpassungsfähigkeit dieser Anlagen ermöglichen schnelle Produktwechsel, was Standzeiten reduziert und die Gesamteffizienz der Produktion erhöht.
3. Kostenreduktion: Da nicht für jedes Produkt eine neue Anlage benötigt wird, können Pharmaunternehmen bei der Einrichtung, dem Platzbedarf und den Wartungskosten einsparen.
4. Sicherstellung der Produktqualität: Diese Anlagen sind häufig mit integrierten Qualitätssicherungsmaßnahmen wie Gewichtskontrollen und Kamera-Inspektionssystemen ausgestattet, die eine gleichbleibend hohe Qualität der Produkte gewährleisten.
5. Regelkonformität: Mehrprodukt-Abfüll- und Verpackungsanlagen sind darauf ausgelegt, sowohl die gesetzlichen Vorschriften als auch die cGMP-Anforderungen (Good Manufacturing Practices) für die pharmazeutische Industrie zu erfüllen bzw. zu übertreffen.
6. Verpackungsflexibilität: Neben der Abfüllung können diese Anlagen auch für unterschiedliche Verpackungsformate wie Vials, Spritzen und Karpulen angepasst werden, um flexibel auf die Anforderungen des Marktes reagieren zu können.
7. Nachhaltige Produktion: Viele moderne Mehrprodukt-Abfüllanlagen sind mit Blick auf Nachhaltigkeit konzipiert. Sie optimieren den Energieverbrauch, reduzieren Abfall und setzen umweltfreundliche Materialien und Technologien ein.
8. Vermeidung von Kreuzkontamination: Modernste Reinigungs- und Sterilisationsverfahren werden häufig eingesetzt, um das Risiko einer Kreuzkontamination zwischen verschiedenen Produkten zu minimieren.
Dieser Vortrag wird die neuesten Entwicklungen und Best Practices im Bereich der flexiblen Mehrprodukt-Abfüll- und Verpackungsanlagen vorstellen und aufzeigen, wie diese Technologien die Zukunft der pharmazeutischen Produktion gestalten können.
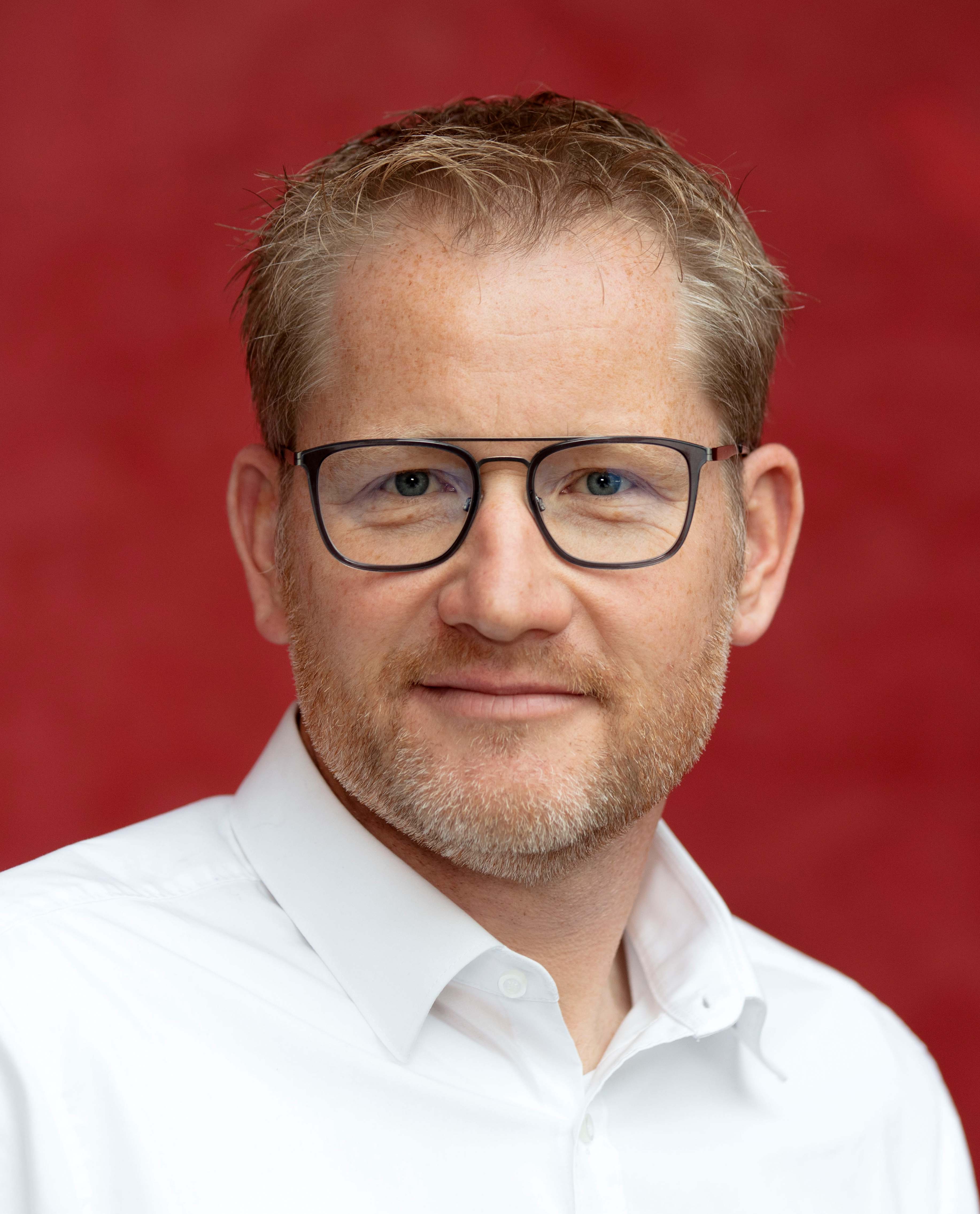