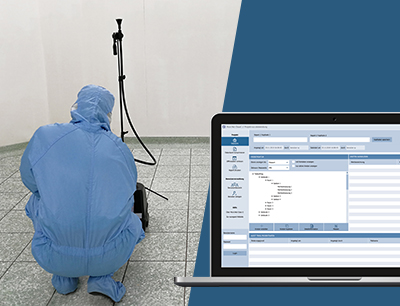
Das diskontinuierliche Partikel-Monitoring für die GMP Reinraumklassen B, C und D wird in der Regel sporadisch ausgeführt und ist eine sehr arbeits- und zeitintensive Tätigkeit, bei der schnell mehrere hundert Messungen pro Monat und entsprechend viel Arbeitszeit anfallen. Die operativen Prozesse werden bei vielen Reinraumbetreibern seit Jahrzehnten auf die gleiche, unveränderte Art und Weise ausgeführt: Messungen werden getätigt, Daten in bspw. Access Datenbanken übertragen und mittels Excel kommentiert und visualisiert. Die geforderte Datenintegrität erfolgt durch die Partikelzähler-integrierte Druckfunktion der Messergebnisse auf Thermopapier. Da die Lesbarkeit von Informationen auf Thermopapier eine begrenzte Haltbarkeit aufweist, müssen alle Messprotokolle aufgeklebt, mit Kurzzeichen versehen, kopiert und archiviert werden. Um eine höhere Aussagekraft zu erhalten oder für die Erstellung von Protokollen werden teilweise Zahlenwerte händisch übertragen oder Durchschnittswerte von Mitarbeitern selbst berechnet. Hierbei stellen mögliche Übertragungs- und Berechnungsfehlern ein Risiko dar. Sollten mobile Partikelzähler verschiedener Hersteller im Einsatz sein, so verkompliziert sich die Gesamtsituation noch weiter und die Arbeitsaufwände sowie das Risikopotential erhöhen sich.
Die Firma eurogard bietet ihren Kunden aus Bereichen wie Pharma, Medizin-, Biotechnologie-, Halbleiter- und Nukleartechnik mit dem Tool Moni.NET Class C eine Lösung an, mit der sich die skizzierten Prozesse hinsichtlich Zeit, Qualität, Kosten und Nachhaltigkeit optimieren lassen.
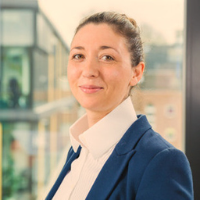