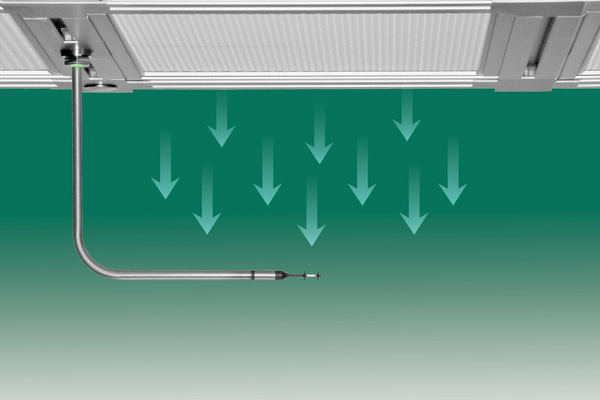
Eine richtungsdefinierte Luftführung in Reinräumen schützt Produkte vor Verunreinigungen und störende Partikel werden sicher abgeführt. Hierzu wird in Reinräumen mit hohen Reinheitsklassen eine gleichmäßige Luftströmung von der Decke zum Boden aufrechterhalten. Der Überwachungsbereich reicht von 0,36 bis 0,54 m/s Strömungsgeschwindigkeit (EU GMP Leitfaden, Annex 1 in Klasse A). Diese Messung erfolgt reinraumseitig nach endständigen Filtern.
Definierte Überdrücke garantieren die Prozesssicherheit in Reinräumen durch Überströmung von einem Raum zum anderen. Diese Überströmung wird üblicherweise mittels Drucksensoren indirekt überwacht. Werden Türen oder Schleusen geöffnet, fällt der Druck oft unter die Messbereichsgrenze des Drucksensors, er zeigt keinen Überdruck an. In dieser Phase liegen dem Reinraumbetreiber keinerlei Informationen (Messwerte) über die tatsächliche Überströmung vor. Es kann jedoch eine Rückströmung und somit ein Kontaminationseintrag vorliegen, ohne dass dies bemerkt wird - trotz korrekt betriebener Druckmessung.
Im Vortrag wird auf die unterschiedlichen Anwendungsfelder der Strömungsmessung im Reinraum eingegangen, die Gegebenheiten vor Ort und die normativen Anforderungen beleuchtet und auch der Zusammenhang zwischen Differenzdruck und Luftströmung dargestellt. Außerdem wird auf üblicherweise verwendete Verfahren eingegangen und häufig gemachte Fehler aufgezeigt.
Einsatzfelder im Reinraum – Überströmung
• Messsituation
• Zusammenhang Druck – Strömung
• Anforderungen
Einsatzfelder im Reinraum – Laminar Flow
• Verwendete Verfahren
• Flügelrad
• Thermische Anemometer
• Positionierung
• Häufige Fehler
• Abgleich und Kalibrierung beim Hersteller
Zusammenfassung
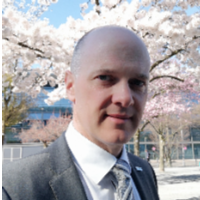