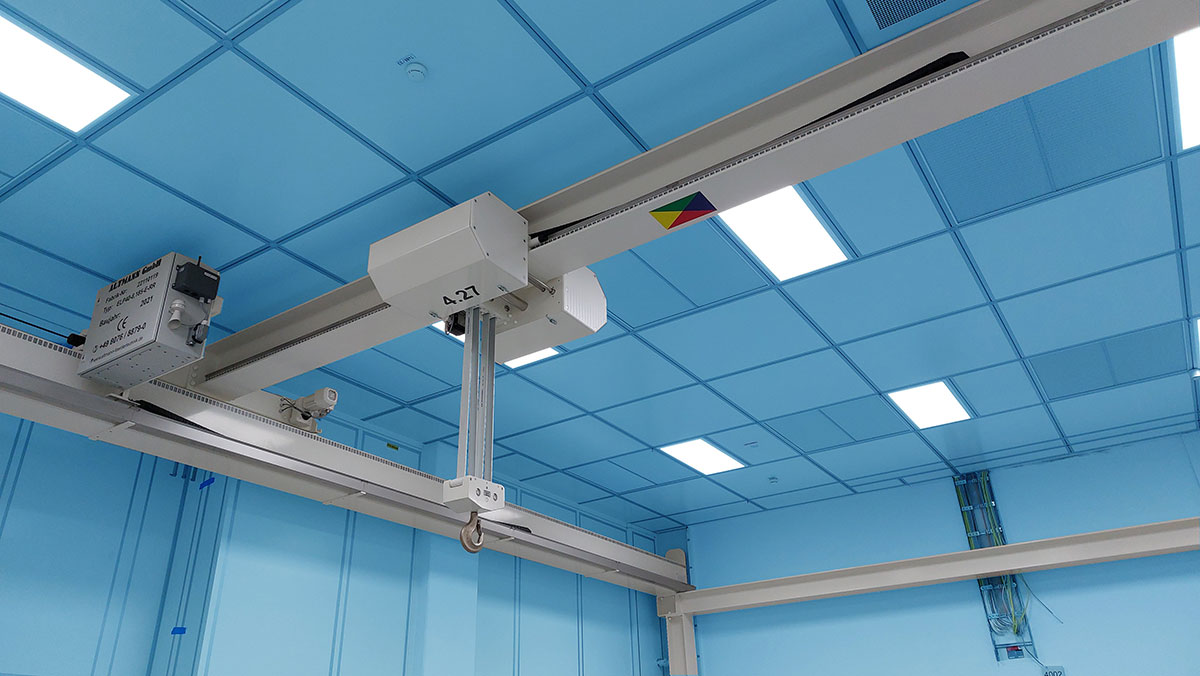
Innovation through recombination - what works better wins in practice
The product solution:
The cleanroom crane with semi-automatic and sway control is currently unique in the cleanroom world and was created in several steps by applying existing technologies and elements to new areas of application.
The focus is on proactively recognizing opportunities and achieving real innovations in the application by combining the existing. The aim is always to create something new that is different and, above all, highly relevant to the market and customers.
After all, what is the point of an innovation that is not accepted by the market and not needed by customers?
To illustrate the innovative power of the cleanroom crane with semi-automatic and sway control in the cleanroom market, it is first important to understand the individual functions and their significance in the transportation process of heavy goods in clean environments. First of all, there is the semi-automatic function, which somehow only sounds "half as good" compared to a fully automatically controlled system. But here, too, we meet a paradox: sometimes half is better than full.
Semi-automatic outperforms fully automatic
To explain: A fully automatic crane, as is already common in many industries, carries out several process steps in a program-controlled, automatic manner. It controls and regulates itself within defined specifications when the appropriate sensors are selected. An intervention by an operator is not required here. The human operator has given way to computer control. However, the area in which such a fully automatic crane operates must be elaborately fenced off, fenced in and equipped with safety access doors. In addition, the programmed processes of the fully automatic crane cannot be interrupted "on the fly" without the need for a costly reset.
A semi-automatic crane, on the other hand, is always the right choice when it comes to recurring work in a consistent chain of process steps that still require the intervention of an operator. A semi-automatic crane is also ideally used in environments that do not allow the danger zone to be completely cordoned off because people are present.
However, the general perception of the word "semi-automatic" is associated with the preconception that it is "nothing half and nothing whole". Quite wrongly, as a closer look reveals. Because the opposite is true: a semi-automatic crane is much more complex to design and program than a fully automatic crane. This is because it takes much more than detailed but static programming to provide the operator with maximum support from the automatic system for routine tasks and still provide the maximum flexibility of a manually operated crane.
Speed up processes, avoid damage
A semi-automatic crane is in constant dialog with the operator. The control system only enables the next correct process step to be approached, such as moving to a target position according to a predefined route. Once the operator has given the go-ahead, the crane moves to the next station. If the release is missing, the crane stops and enters a safe system state. If the operator moves the semi-automatic crane into a collision area during manual operation, the crane also stops automatically.
In addition to these safety-related benefits, the use of a semi-automatic crane also shortens throughput times and speeds up the process steps. It also increases the effectiveness of in-house transportation and reduces the workload of the operating personnel.
Similar to a person's sensory organs, the sensors integrated into the semi-automatic system detect the process status. They assume the central role in the control system and transmit the collected data to the control software, which regulates the process sequence. Nevertheless, the operator is still ultimately in control of the semi-automatic crane, as they must first approve the programmed work steps using an enable button.
Precise and automated work processes
This type of cleanroom crane is equipped with a programmable logic controller (PLC) and a three-axis positioning system that allows a positioning accuracy of +/- 1 millimeter per axis. A semi-automatic approach is possible for stored positions, which means that expensive system parts can be easily changed. In addition, collisions and the resulting damage to such system parts are avoided from the start by the fact that it is only possible to move out of the stored positions in an approved direction. In order to comply with cleanroom class ISO 5, the semi-automatic crane has an easy-to-clean surface and has no sharp-edged components such as screw heads, which makes cleaning extremely easy.
Particularly high demands are set on the control and programming of semi-automatic cranes. As the operator must be able to intervene in the process at any time and the software must only allow logical commands to prevent human error, the control system must constantly monitor the status of the crane and the process.
A semi-automatic crane offers the following features at a glance:
- millimeter-precise positioning of the crane in all axes, regardless of load capacity, span and travel speed,
- precise picking up and setting down of loads,
- Control of the semi-automatic crane by means of a programmable logic controller (PLC) and frequency converters integrated in ProfNet,
- Travel speeds of up to 63 m/min,
- Accelerations of up to 1 m/s² using friction drives (i.e. without rack and pinion drives)
- Transmission of the applied load or other process variables to a higher-level control system,
- High-precision load measurements.
Millimeter-precise and vibration-free thanks to sway control
The above-mentioned advantages of a semi-automatic crane are supplemented by a further dimension when combined with the innovative technology of electronic sway control. This sway control ensures that no inertia-induced vibrations occur and that the crane operator does not have to perform any compensating movements - neither during acceleration nor braking. This completely prevents the load from swaying. It is particularly remarkable that this is possible regardless of the speed and hook position of the load. At the same time, the risk of accidents due to swinging movements is reduced to a minimum, both when moving the load and when stopping. Another advantage is the avoidance of increased abrasion, which is unavoidable every time the crane accelerates and brakes. The resulting reduction in particle discharge is essential in cleanroom environments. Compliance with the requirements of ISO class 5 is therefore guaranteed.
Thanks to the electronic sway control, the crane hits the desired target coordinates with pinpoint accuracy. This is achieved without the hook being subjected to further vibrations during travel or after the crane has come to a standstill, or making unpredictable compensating movements during travel or after the crane has come to a standstill. This enables much more precise and, in particular, faster work. Without sway control, precise positioning of the object takes a lot of time, requires both calmness and skill and also makes everyday work much more difficult.
In many cases, it is also very important to ensure that a load is stopped precisely without swinging and that the desired target point is not exceeded, as otherwise damage may occur to the usually valuable load or the target object. However, there is no guarantee of this when positioning objects without sway control. In addition, the swaying of the load increases the risk of accidents for the people involved.
More efficiency in the operating process
If the technical and functional benefits of a semi-automatic crane with sway control are already impressive, criteria such as easy to use and therefore efficiency in the operating process and sustainability in use should not be underestimated by customers.
As far as efficiency is concerned, it is obvious that the operator of the semi-automatic crane is supported to the maximum by the technology and can therefore work quickly and yet safely. There is no need for time-consuming positioning of the transport parts, which are usually extremely valuable and therefore difficult to replace in the event of damage. The operator is relieved of the worry of making mistakes and thus taking on heavy responsibility. At the same time, the routine processes are taken over by the technology.
This is particularly important with regard to changing employee structures. According to studies, the staff of the future will want maximum support from technology in order to bear less responsibility for any errors. On the other hand, however, employees do not want to degenerate into meaningless machine observers. Semi-automation is the perfect mix here, as it does not replace jobs, but provides machine support for those jobs for which it has become or will become difficult to find qualified staff.
Sustainability in product use
For you as a customer, the semi-automatic crane offers the great benefit that the hardware and software installed in the crane allows all conceivable adaptations and changes to be made as the product cycle progresses. For example, an article database can be created if required and used for the transportation of changing yet recurring workpieces. The configuration of the sway control and the programming of the transport path are also positively influenced by this. With the purchase of the crane, the source code belongs to the customer, who can adapt it to their own wishes and requirements.
Innovative and customizable
Overall, the cleanroom crane with semi-automatic operation and sway control offers a whole range of highly innovative features that make it ideal for many heavy-duty transport tasks in cleanroom environments. To date, we have already built cranes of this type with a lifting capacity of up to 30 tons, a span of 30 meters and a speed of 60 meters per minute according to customer requirements.
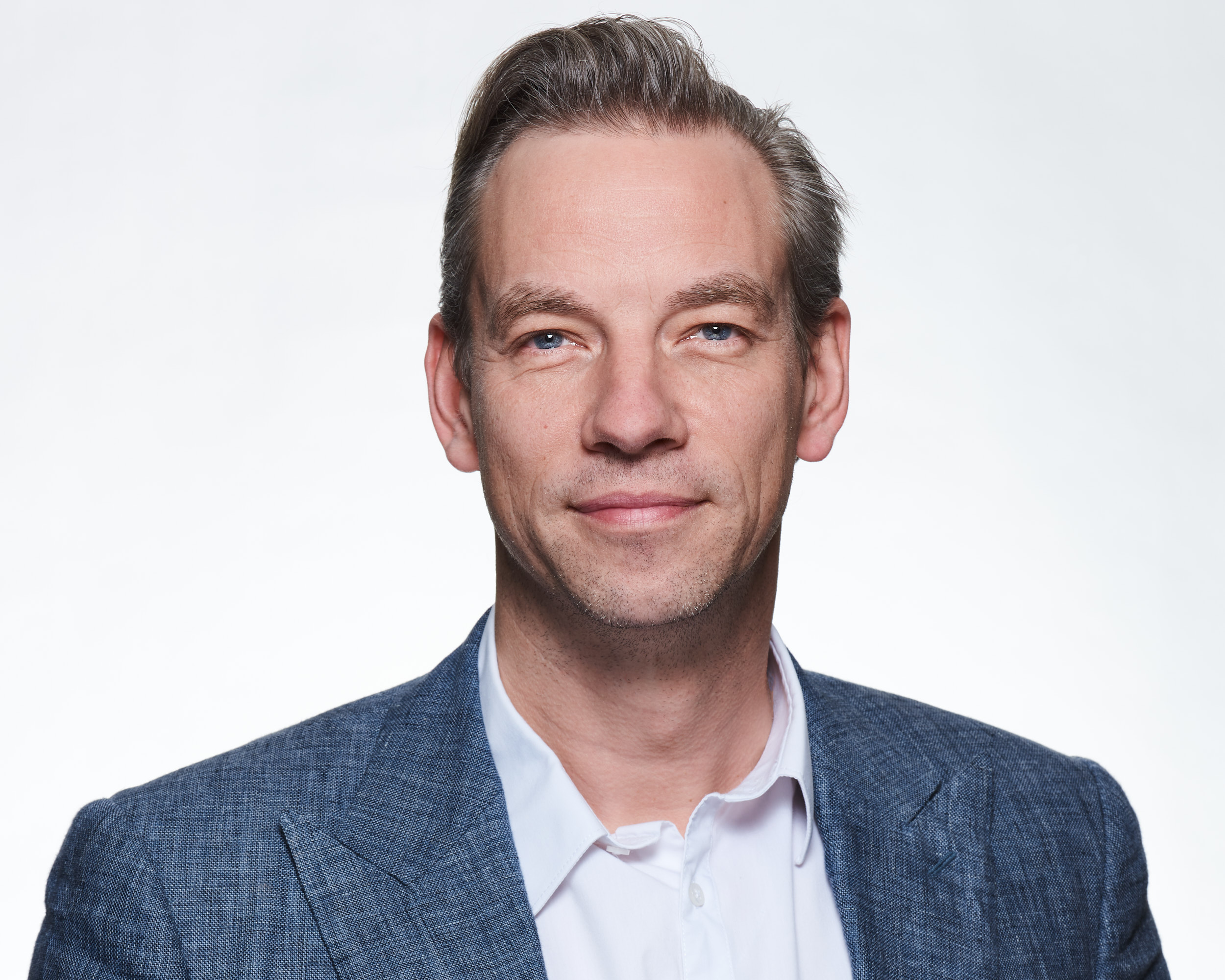